Send Mail to Jehanne Simon-Gillo
Jan Boissevain and Jehanne Simon-GilloFebruary 22, 1996
PHENIX-MVD-96-7
This document is in response to the Progress Report generated by ESA-DE in
January 1996, "ESA-DE PHENIX MVD Design Review", written by Lucie Parietti,
Chris Potter, Tim Thompson and Dick Martin. The Progress Report was divided
into seven sections which dealt with four topics:
- Electronics Cooling
-
Fluid-Induced Vibrations
- Gravitational Displacement
- Hydroscopic
Expansion of Rohacell.
We have studied the conclusions and recommendations
suggested by ESA regarding each of the four topics and have addressed them
below. Each section corresponding to one of the ESA topics, is broken up as
follows: - Summary: brief summary of the ESA report on that particular topic
- Comments: Statements which clarify already complete R&D tests or
mechanical plans, as well as additional tests which we agree to perform in the
future
- Future tests: Additional tests which we propose be conducted by
ESA-DE. This section is divided into two lists. The "Class A" tests are those
which we feel could be started right away, assuming that we agree on the ESA
financial and time estimates. The "Class B" tests are those which we will
likely want to be conducted in the near future. We would like to request from
ESA, estimates which describe the costs and time needed to perform these tests.
Please make separate estimates for the "Class A" and the "Class B" tests.
The following concerns were expressed and suggestions were made:
- Utilize a heat spreader on the base of the MCM to minimize the temperature
non-uniformity across the MCM.
- Investigate possibility of lowering plenum inlet air temperature via a
water chiller.
- Construct a full-scale prototype air cooling system in lab with resistive
strip heaters and measure temperature of MCM and air.
- Study thermal stratification of flow in cooling plenum.
- We agree that we should utilize a heat spreader to minimize the temperature
non-uniformity across the MCM.
- We always intended to use a water chiller if air cooling is the
technology choice.
- We already have constructed full scale mechanical prototypes of air-cooling
systems in which we simulate heat loads and measure air and MCM temperatures.
Please refer to NIMA 345(1994)284. General agreement exists between the ESA
cooling calculation results and the MVD results described in the article. We
have also built a six layer cooling prototype and an MVD note is currently
under construction. We recognize the importance of building a final full scale
prototype of our cooling system once a technology choice is made and the
mechanical design is complete.
- Mechanically, no further progress can be made concerning a cooling
technology choice until progress is made on the MCM technology and electronic
component characteristics. However, we did perform some simple cooling
estimates based on the current knowledge of the MCM size, power dissipation and
cooling calculations from the ESA report. These results can be found in "Air
Cooling Status Report", PHENIX-MVD-96-4.. They indicate that air
cooling is still a feasible option.
2.3.1 Class A
- Study distortion of truss structure as a function of inside environment
temperature.
- Study efficiency of Aluminum Nitride MCM substrate.
2.3.2 Class
B
- Study feasibility of cooling the silicon detectors with electronics cooling
system vs. independent cooling system (After cooling technology choice).
- Studies to maximize efficiency of cooling system design (After
cooling technology choice). For example, adding fins to MCM in air cooling.
- Study thermal stratification of flow in cooling plenum. (IF air
cooling is technology choice.)
- Finite element calculation of final cooling system with final electronics
dimensions and characterizations (After cooling technology choice).
- High velocity cooling air may induce vibrations that create noise pickup in
the electronics and deterioration of Rohacell plenum mounting grooves.
- Measure velocity and pressure in the final plenum as a function of time and
frequency. ESA would then be able to perform a COSMOS finite element analysis
to determine normal nodes of vibration and possible resonances. ESA also
offered to aid in measurements of induced-vibrations with the use of
transducers and anemometers.
- Exercise care when designing cooling loop to avoid high turbulence levels.
- Attention to design MCM configuration to produce uniform heat load
transversely in the plenum.
- We are aware that air induced vibrations may lead to noise pickup and
deterioration in the Rohacell plenum. With the use of an accelerometer, we have
measured in three dimensions the displacement of the prototype plenum as a
whole and a centrally located MCM in this plenum. Preliminary results indicate
that all measured displacements are less than 100um. There is some evidence
that the plenum and centrally located MCM enter resonant states in narrow and
different velocity ranges. This may potentially be a concern, mechanically, but
we do not feel it is efficient to study the problem further until a cooling
technology choice has been made and the cooling system fully designed, as the
degree of mechanical instability introduced will largely depend on the final
mechanics of the plenum, assuming air cooling is the technology choice.
- We have studied the effect of adding mechanical robustness to Rohacell by
coating it with a thin layer of parylene. R&D results on this subject can
be found in "Parylene Conformal Coating for Rohacell", PHENIX-MVD-95-12. If air
cooling is the technology choice and if it found that the induced vibrations do
deteriorate the Rohacell at the MCM mounting groove, then we may consider
coating the Rohacell plenum with parylene.
- Of more importance is the sensitivity of the electronics to induced
vibrations. The effect of mechanical vibrations on the performance of the
electronics will be studied in the lab and during a beam test in April 1996 at
the AGS.
3.3.1 Class B
- We agree that we should construct a final plenum and make velocity and
pressure measurements once the cooling design is complete so that ESA can
perform a COSMOS finite element analysis. We would be pleased to work with ESA
in making these measurements.
- Simulations to optimize plenum performance.
- Evaluation to optimize design of plenum transitions (adapters) and cooling
loop.
- Study mechanical deterioration of Rohacell due to induced vibrations and
effect of Parylene coating.
- ESA calculations indicate that the MVD detector assembly does not
experience any significant gravitational displacement and that the mechanical
design is acceptable.
- Expansion of Rohacell due to moisture absorption will cause distortions in
support framework.
- Expansion of Rohacell due to moisture absorption will cause high stresses
in the area of the foam-silicon glue surfaces. Small changes in humidity may
result in values of stress that exceed tensile stress of foam.
- "Potentially serious problem exists, with potential for non-functioning of
the assembly."
- We should bond Rohacell frame around single silicon strip and expose to
humidity cycles to study cracking, separation, tearing from foam.
- ESA should make stress-strain curve for Rohacell to obtain Young's modulus
and elastic limit for foam.
- We should make more careful determination of moisture coefficient of
Rohacell. Allow expansion to reach equilibrium and study time-dependent
behavior. Measure foam at ambient conditions of New Mexico then expose to
higher humidities, as high as 100% relative humidity. Tests should be performed
with and without coatings.
- We should consider testing parylene coating to measure effect on short term
and long term expansion.
- Consider flexible bonds between silicon and foam to minimize effects from
distortion and stresses.
- Consider alternative materials to foam.
- We feel that many valuable suggestions have been made regarding additional
tests which we should perform and methods in which we can improve the
environmental tests already conducted. However, we do not feel that the
use of Rohacell in the MVD cage assemblies poses a "serious problem". We would
like to emphasize that our preliminary results from environmental tests of
Rohacell indicate that we do not approach any mechanical or physics tolerances
("Influence of Silicon Wafers on the Expansion and Contraction of Rohacell
Cages when Exposed to a Changing Environment, PHENIX-MVD-95-11). We have not
yet begun to study the stress at the silicon/foam joint and we acknowledge the
concerns described by ESA. We are pleased to see that several options exists
which we can explore to minimize this effect.
- Results from ESA calculations are based on cycling relative humidity
between 30-80%. It is intended that the MVD operate in a stable and controlled
environment with relative humidity ranging between 30-40% (the same conditions
under which the silicon/cage sections were assembled). Of course, it is
important that we understand how the Rohacell behaves at high humidity in case
of enclosure failure. It is expected that the relative humidity of the
experimental hall be less than 40%, therefore we are more concerned with
accidental exposure prior to installation in the experimental hall (such as
shipping).
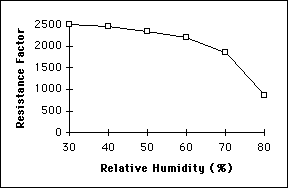
Figure 1. Water Diffusion in Rohacell Foam
- The data shown in figure 1 was obtained from the Rohacell Manufacturer.
This plot shows that the water diffusion into Rohacell in the case studied by
ESA (30-80 %cycling in humidity) is nonlinear . Assuming linear behavior and
extrapolating ESA results to real operating conditions will then lead to
pessimistic results.
- We do not currently intend to test single frames of Rohacell as suggested.
It is not clear as to what additional information would be obtained in
comparison to past tests (PHENIX-MVD-95-11) and future tests described below.
We are willing to reconsider if the benefits of this test are made more
clear.
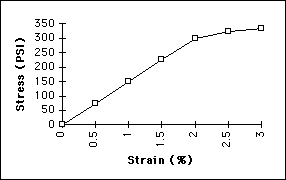
Figure 2. Rohacell Stress vs Strain
- Figure 2 shows data from the Rohacell Manufacturer. The % Strain in the
plot refers to %
L/L. The experimentally measured number given to ESA
(on the order of 1%) is a worse case situation and is still well within the
elastic properties of the Rohacell (falls on the linear portion of plot in
figure 2).
- Several detailed environmental tests on Rohacell cages have already been
performed (See PHENIX-MVD-11, PHENIX-MVD-12).
- Our approach is already to begin the tests at the ambient conditions of New
Mexico then increase the humidity.
- We have always studied the time dependence of the foam behavior.
- We agree that we may not have allowed the expansion to reach equilibrium
before changing humidity- this will be investigated.
- We do not feel that it is necessary to carry the tests to 100% relative
humidity which can be complicated. It is unrealistic to expect that the MVD
will ever be exposed to 100% relative humidity unless Jan drops it into the
bath tub.
- We intend to test coated and non-coated cages.
- We wish to repeat our environmental tests with a partially populated
silicon cage so that the results can be directly compared to ESA predictions
(Our previous results are on a fully populated cage).
- We wish to add the change in length to our measurements; in the past, we
concentrated on change in radial and width dimensions.
- We have already tested the short-term effect of parylene on Rohacell
("Parylene Conformal Coating for Rohacell, PHENIX-MVD-95-12). We agree that we
should test the long term effect of parylene on Rohacell.
- We agree that we should investigate options which will lead to a flexible
bond at the silicon/foam joint and that we should also investigate mechanical
design changes which would minimize stress at this joint. We intend to evaluate
glue candidates during the Summer of 1996.
- We feel it is unnecessary to consider alternative materials to the foam as
our results indicate that we do not approach mechanical or physics tolerances
and options exist which can minimize stress at the silicon/foam joint. We did
estimate the thickness of a cage made of aluminum which has the same radiation
length as the Rohacell cage. The aluminum thickness would be 15um (0.0006").
Such a cage would likely be difficult to construct.
5.3.1 Class A
- Stress-strain test of Rohacell. Please inform us of sample size
requirements.
5.3.2 Class B
- Perform simulations with 0.5mil parylene coated cage (after we have
evaluated long-term effect of parylene).
- Perform simulations on proposed design changes and glue candidates that
minimize stress at silicon/foam joint.